World Class Silversmithing in Setedal
- Marion Solheim
- Jun 6
- 3 min read
Updated: Jun 18
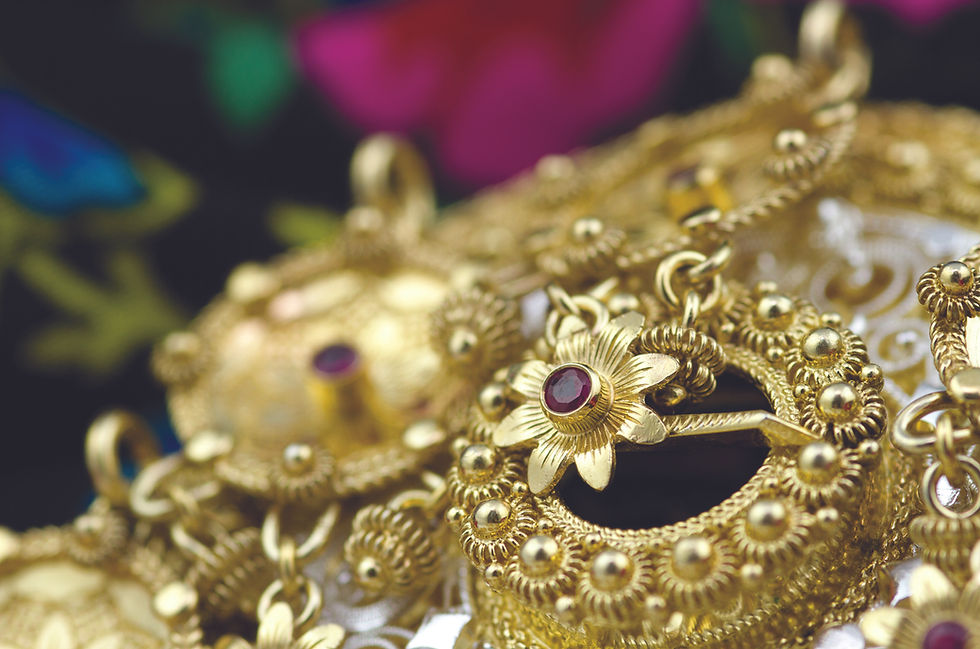
Silversmithing has long been a celebrated tradition in Setesdal. For centuries, skilled artisans have crafted exquisite brooches, buttons, and jewelry for the region’s bunads – and more. To this day, Setesdal’s silversmiths are in the elite league.
Traditions Rooted in Viking Times
The Vikings had a thing for silver adornments, creating intricate and stunning jewelry that remains difficult to replicate even with modern tools. Their pieces were crafted by filigree silversmiths, who used thin wires and tiny beads to create delicate, unified designs.
Today, filigree craftsmanship is most famously seen in bunad brooches (søljer), but the Vikings also embraced this intricate art form for their jewelry.

Over time, the demanding craft of filigree was gradually replaced by cast silver jewelry, which was easier and less expensive to produce. In urban areas, silversmiths organized themselves into guilds from the 1500s onward, and practicing the craft without guild membership became illegal. In the villages of Setesdal, far away from the cities, independent silversmiths were branded as outlaws and risked punishment for their craft. This continued until the introduction of a new crafts law in 1839.
A Sparkling Industry in Setesdal
The Kongsberg Silver Mines, established in 1623, operated for over 300 years and supplied much of Norway’s silver. Some of the silver that made its way to Setesdal was likely stolen from the mines. Theft of the metal was not uncommon, and lumps of silver often found its way into communities across the country.

In the latter half of the 19th century, the art of filigree brooch-making really reached Setesdal, sowing the seeds for an entire, little industry. Silversmithing was often a supplemental trade. Aspiring artisans began by crafting their own tools. They made pliers, clamps, files, and saws; these were essentials. As were larger wooden tools like the draw bench for making silver wire. To save on costs, silversmiths relied on themselves and their skills. Work was typically done in the living room, often at a table beneath the sole window to ensure light one could work in. Soldering was performed using a paraffin lamp fitted with a long spout, which held a paraffin-soaked cloth. A blowpipe was used to achieve the high temperatures needed for soldering. This was something thar required skill and precision. Stay away, kids!
Family members often helped prepare the numerous tiny components needed for a brooch, but it was the master silversmith who soldered them into the finished piece. The widespread use of Setesdal bunads ensured a strong local market for these beautiful silver brooches. The same can be said for the present, actually.

Today: Premium Craftsmanship and the Silver Village of Rysstad
The tradition of filigree silversmithing in Setesdal is alive and thriving. In Valle, a nationwide educational program in goldsmithing emphasizes filigree work, preserving this traditional craft for future generations.

Young, passionate artisans are carrying forward the legacy of the master silversmiths, creating stunning jewelry.
Setesdal is often called the Valley of Silversmiths, and the village of Rysstad in Valle is at the heart of it all. The Rysstad family has deep roots in this tradition. Today, both third- and fourth-generation silversmiths carry on the legacy of filigree work at Rysstad Sylv, one of the most important artisan workshops in the south of Norway. Tradition is honored here in the truest sense.
The silver workshop and showroom are now integrated into the Sølvgarden Hotel, offering visitors a unique glimpse into the world of Norwegian filigree artistry.
In the hands of the Setesdal’s silversmiths, silver becomes more than ornaments. It becomes heritage made visible.
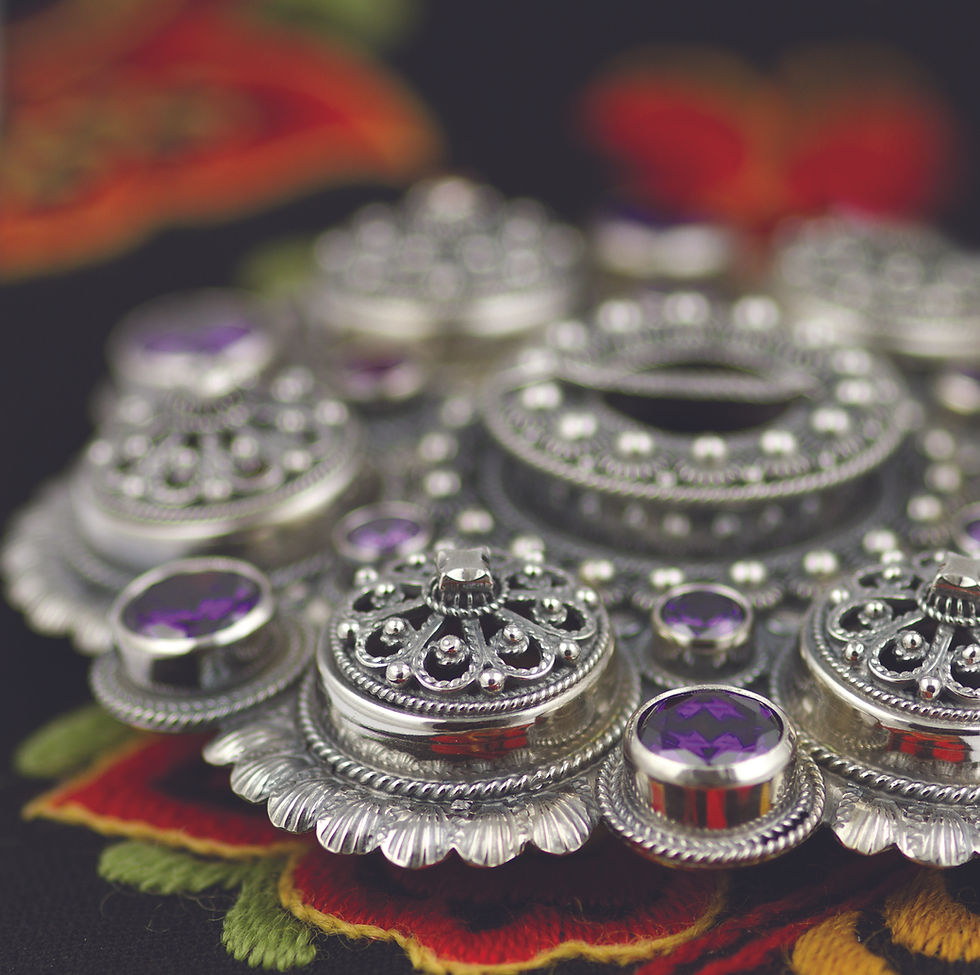
Sources: